Posted by admin , on Sep, 2015
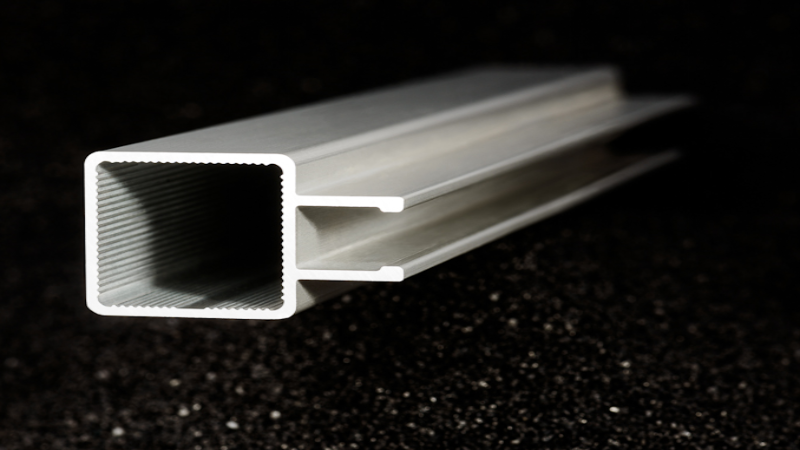
Aluminum extrusions utilize the unique properties of aluminum alloy and are used in many applications. These extrusions can be specialized using any die or customized shape. Choose an experienced manufacturer and almost anything can be created using custom aluminum extrusions.
Beginning the Process
For a company to produce custom aluminum extrusions, they must begin with a purely aluminum billet (or log). The billet is machine-fed into a heating device that will cause the aluminum to become malleable at around 900°F. Once the billet is hot enough to work with, it is removed and cut to the necessary size for the shape it will become.
Shaping the Billet
Once cut to the right size, the billet is forced into a container and up to 3000 tons of pressure will be applied to it to squeeze the aluminum through the die. The die is any shape necessary for the project. The pressure applied by this machine allows the aluminum to take the shape of the die before it exits the other end.
Finishing the Process
When the billet exits the machine, it is still fairly malleable and must be cooled for it to harden properly. It must first be cooled to room temperature where it will remain soft so it can be cut. The aluminum is then cut into the specified number of pieces and then cooled further to resume a hardened state. As they cool, the aluminum pieces will shrink which alters the shape. Each piece must be stretched back into the proper shape once they are cooled. To achieve complete hardness, an artificial aging machine is often used.
Ensuring Quality
The best way to ensure that custom aluminum extrusions are of high quality is to do your research on the manufacturer. You want to use a manufacturer that is experienced with many different shapes and sizes. You also want to make sure that they have engineers available to customize any out-of-stock requirements. Finally, follow-up on the company’s testing process to confirm that they make sure every spec requirement is met before releasing any extrusions.