Posted by Zoe Geoffrion , on Sep, 2018
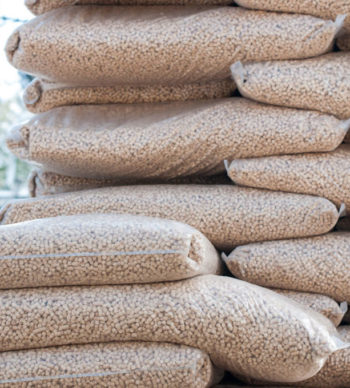
For plenty of companies, pharmaceutical packaging can be an afterthought. With about 50 percent of pharmaceutical recalls attributed to product labeling errors or packaging mistakes, companies can’t afford to ignore errors in their pharmaceutical packaging workflow any longer.
Here’s why it matters.
Ensure patient safety
Errors in labeling could lead to overdose and misuse, which, in turn, can result in negative side effects. That’s how essential it is for a company’s prescription labels to be accurate. Any errors could worsen a patient’s condition or result in one, Xtalks says. Prevent risks to patient safety by partnering up with the right supplier for pharmaceutical packaging.
Prevent compliance issues
The FDA has set clear guidelines for this type of packaging. The guidelines provide a list of items that the label must have. Failure to provide those items will lead to compliance issues with the FDA, which could mean recalls. Keep these problems from happening by taking steps to improve your product packaging. Start by hiring the right supplier.
Save on costs and time
Recalling a product can mean a ton of costs. That’s money you can use for other aspects of your business. The cost of the recalls will also affect your returns and bottom line. That’s not to mention the time and effort it will take to deal with these issues. Not only will you need to investigate the problem, but you must also come up with an effective and efficient resolution to the problem as well. That’s time and money you could have spent on developing new products.
Maintain reputation and image
Recalls hurt the reputation and image of your brand and business. That’s going to reduce consumer satisfaction and trust in your products, which will further cut sales and returns. Prevent the negative publicity by fixing any packaging problems and working together with the right supplier.